Engraving Plastics: Part Two
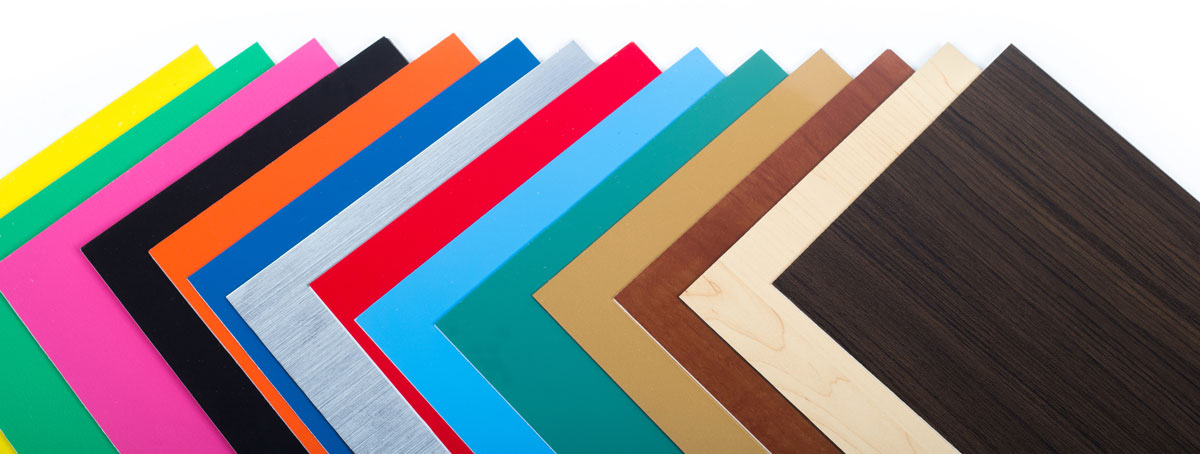
This is the second in a five-part blog series all about engravable plastic sheet materials. Click here for part one about what makes a plastic laser engravable and other characteristics of engravable plastic sheet.
Understanding how plastic engravable sheet products are constructed can go a long way to helping you determine what material to use for your next project. There are multiple options available, using terms such as front engravable, reverse engravable, two-ply, three-ply, and mono sheet. This blog will take a look at those differences so you can make an informed decision when buying engravable sheet plastic.
The difference between front and reverse engravable sheet plastic
Front engravable (or first surface) plastic is a type of plastic material that can be engraved or etched from the front surface. It is typically used for creating signs, nameplates, awards plates and other types of identification and labeling applications. The material is made from a durable plastic that is designed to resist fading, cracking, and peeling, even with prolonged exposure to the elements.
The front surface of the plastic has a colored layer (cap) of thin plastic or foil that is engraved using a laser engraving machine or other type of engraving tool to reveal the color of the base layer (core). The engraved surface typically has a contrasting color which provides good visibility and makes the text or graphics stand out.
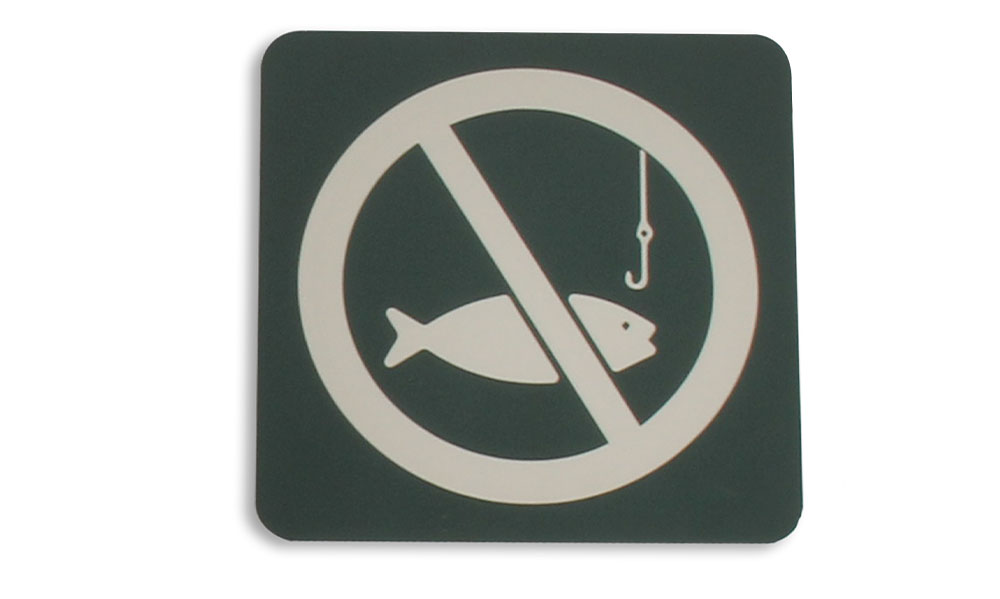
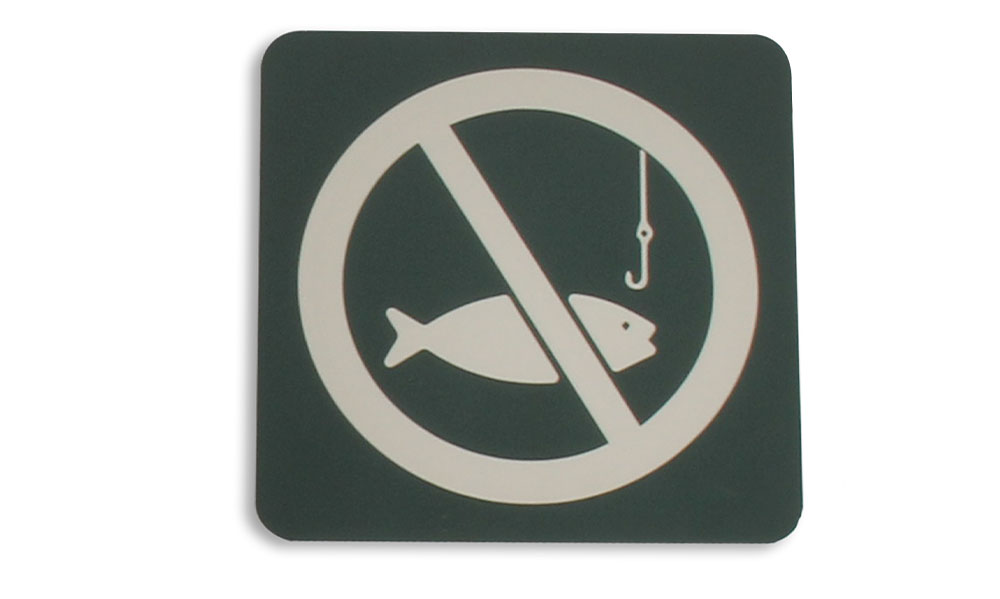
Front engravable plastic is available in a wide variety of colors, sizes, and thicknesses, making it a versatile material for many different applications. It can be used for both indoor and outdoor signage, and is commonly used in commercial, industrial, residential, and hobby applications.
Reverse engravable plastic is a type of plastic material that can be engraved or etched from the back surface, which creates a raised, embossed effect on the front surface. It is also known as backwards or sub-surface engraving.
The material used is typically made from a high-quality acrylic or ABS that is designed to provide a clear, crisp image. The back surface of the plastic has a thin, colored foil layer that allows it to be engraved using a laser or rotary engraver. When the engraving tool removes material from the back surface, the engraving shows through the clear front of the plastic. The front area of the engraved piece remains flat and unmarked, allowing for a smooth finish that’s easy to clean. The back, engraved area can be filled with any acrylic paint, another sheet of colored plastic, or vinyl to create a truly unique sign and color combination.
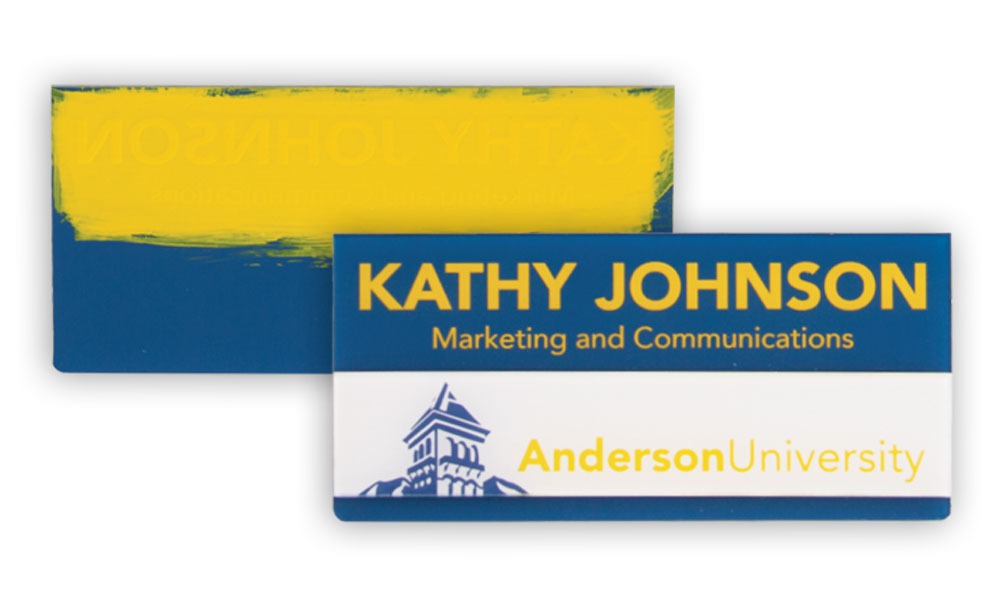
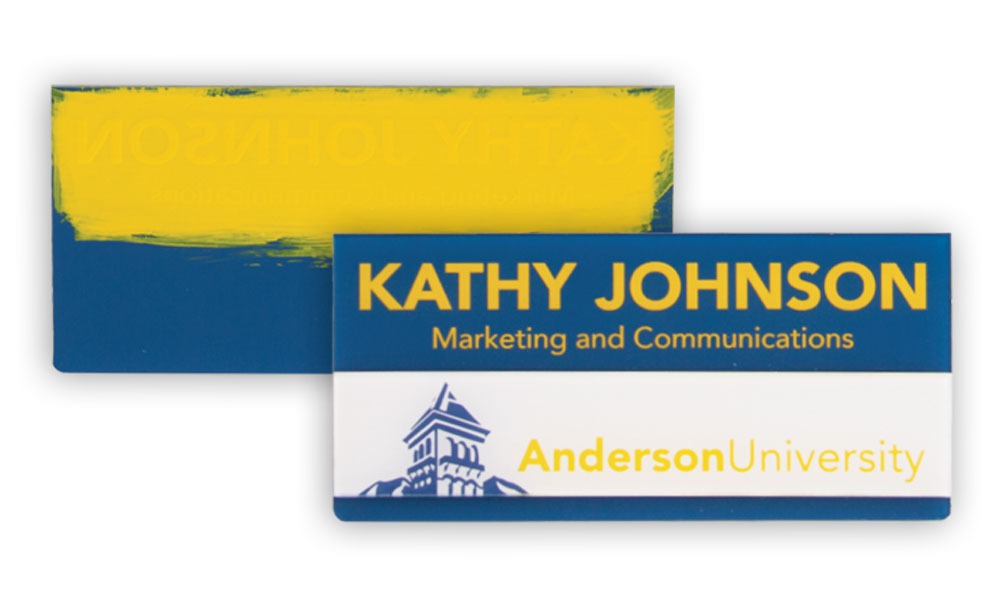
Reverse engravable plastic is often used for creating custom nameplates, signage, and plaques. The raised lettering or graphics on the front surface provide a unique and professional look, and the durability of the material ensures that the engraving will remain legible for years to come. This type of plastic is commonly used in industrial settings, but it can also be used for decorative purposes in commercial and residential settings.
Defining two-layer, three-layer, and mono sheet engravable plastic
Two-layer and three-layer engravable plastic sheets are two different types of materials used for engraving, marking or labeling applications. The main difference between them is the number of layers they consist of.
A two-layer engravable plastic sheet typically has a top layer of a contrasting color, such as white or yellow, that is bonded to a base layer of a different color, such as black or red. When the top layer is engraved or cut through, the base layer is revealed, creating a high contrast image or text. This type of material is often used for signage, identification tags, and nameplates.
On the other hand, a three-layer engravable plastic sheet consists of a top layer, a core layer, and a bottom layer. The top layer and bottom layer are usually of the same color, while the core layer is a different color. When the top layer is engraved or cut through, the core layer is revealed, creating a contrasting image or text. By engraving through the top layer of either side of the sheet, you can easily create a two-sided sign or nameplate for wall flag, hanging, and post install applications.
Finally, you may see items listed as mono sheet, single layer, or single ply engravable sheets. These products consist of a single layer with no cap layer. Their primary use is to be fabricated into applied pictograms for ADA signs, cut into single color letters, shapes, or numbers, or to be used as backer pieces for other applied images and graphics.
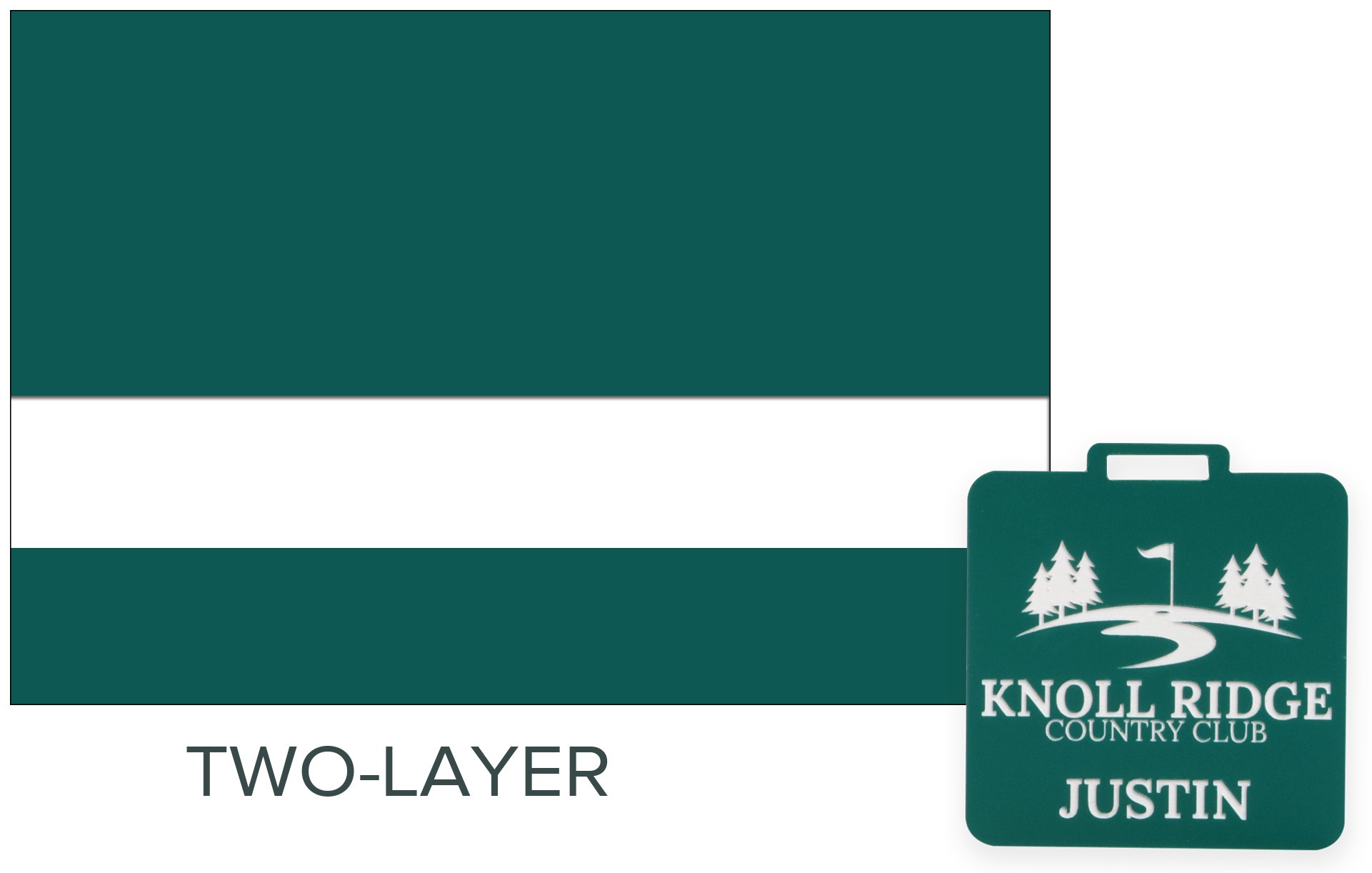
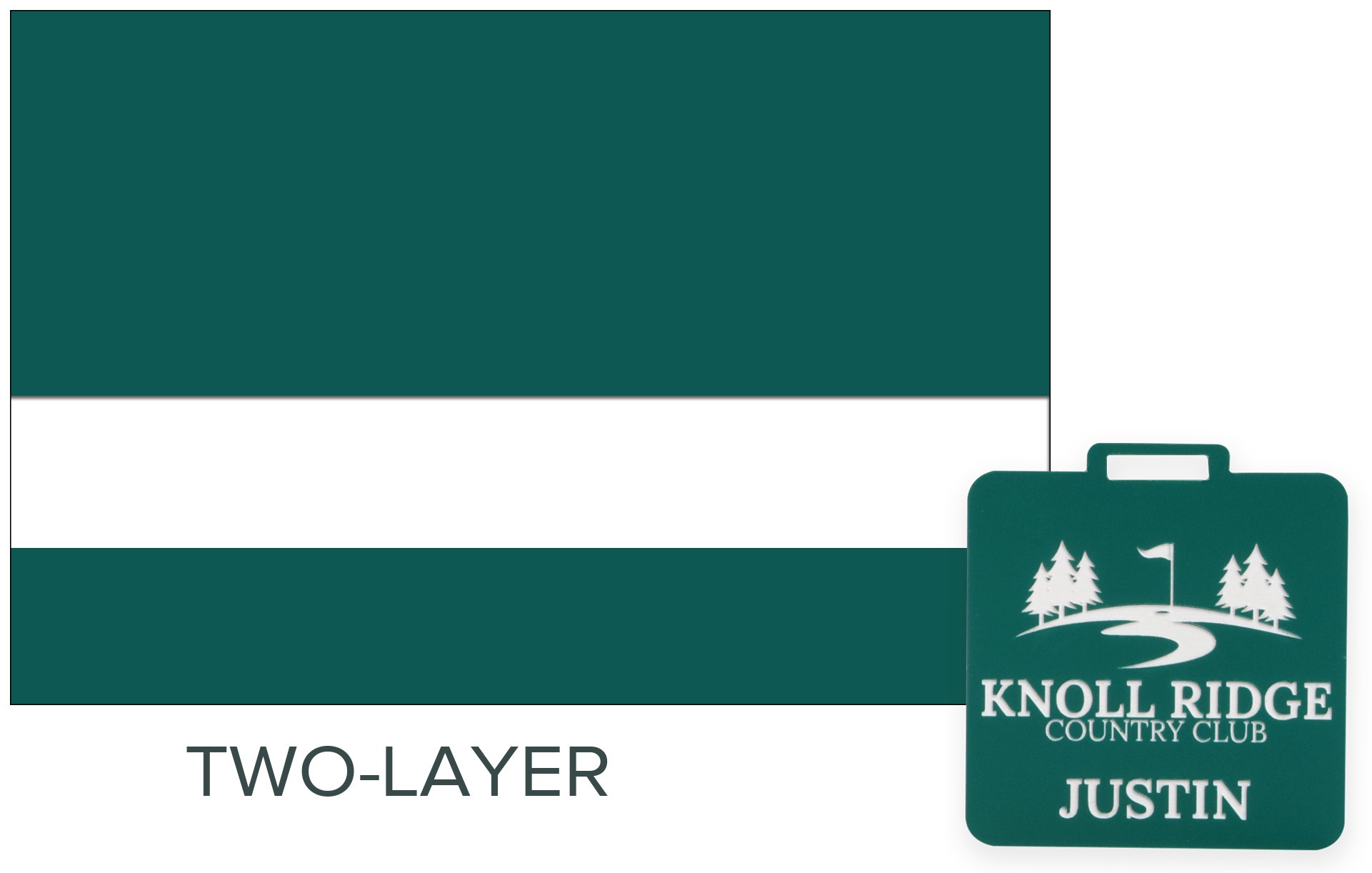
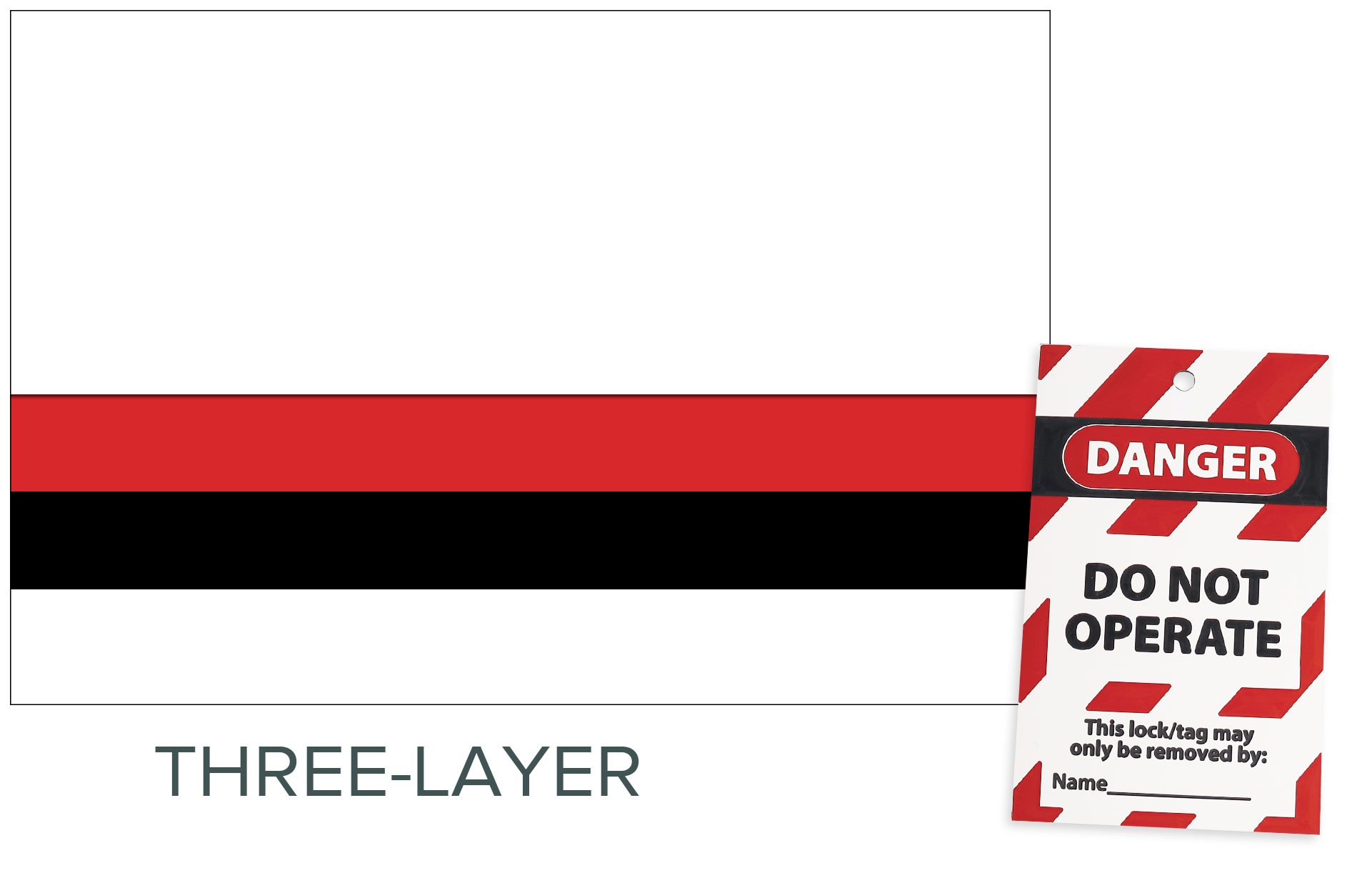
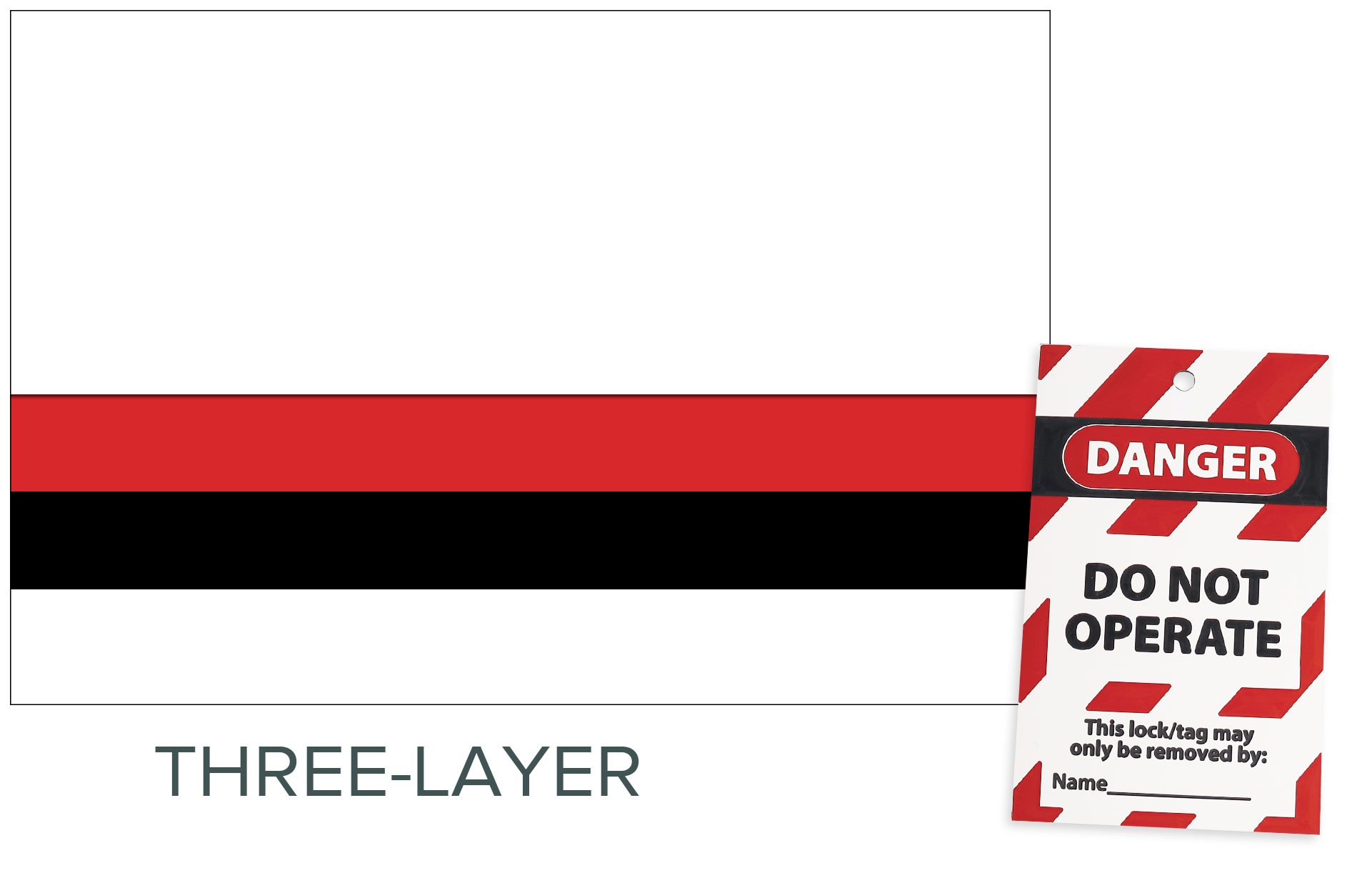
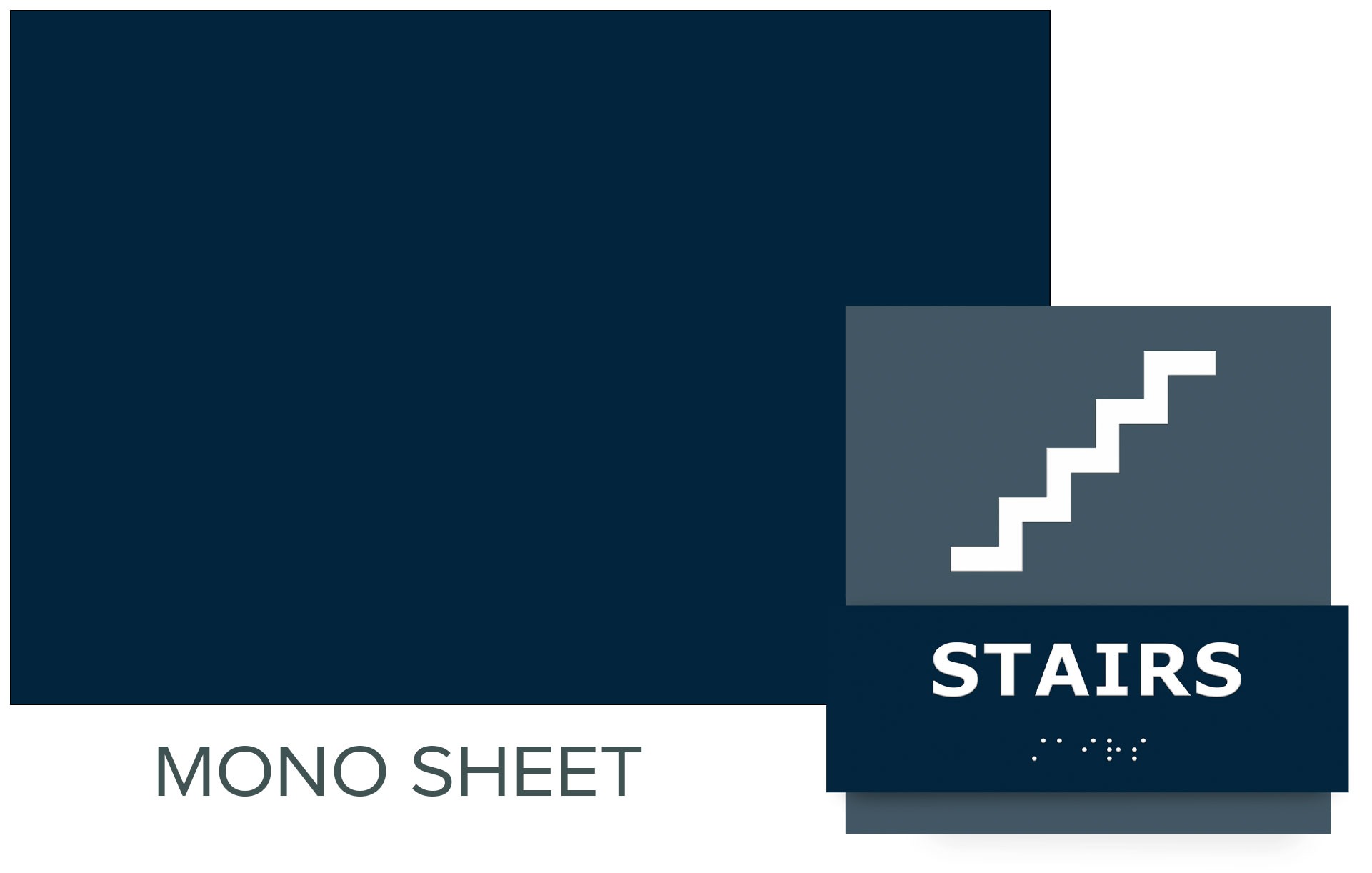
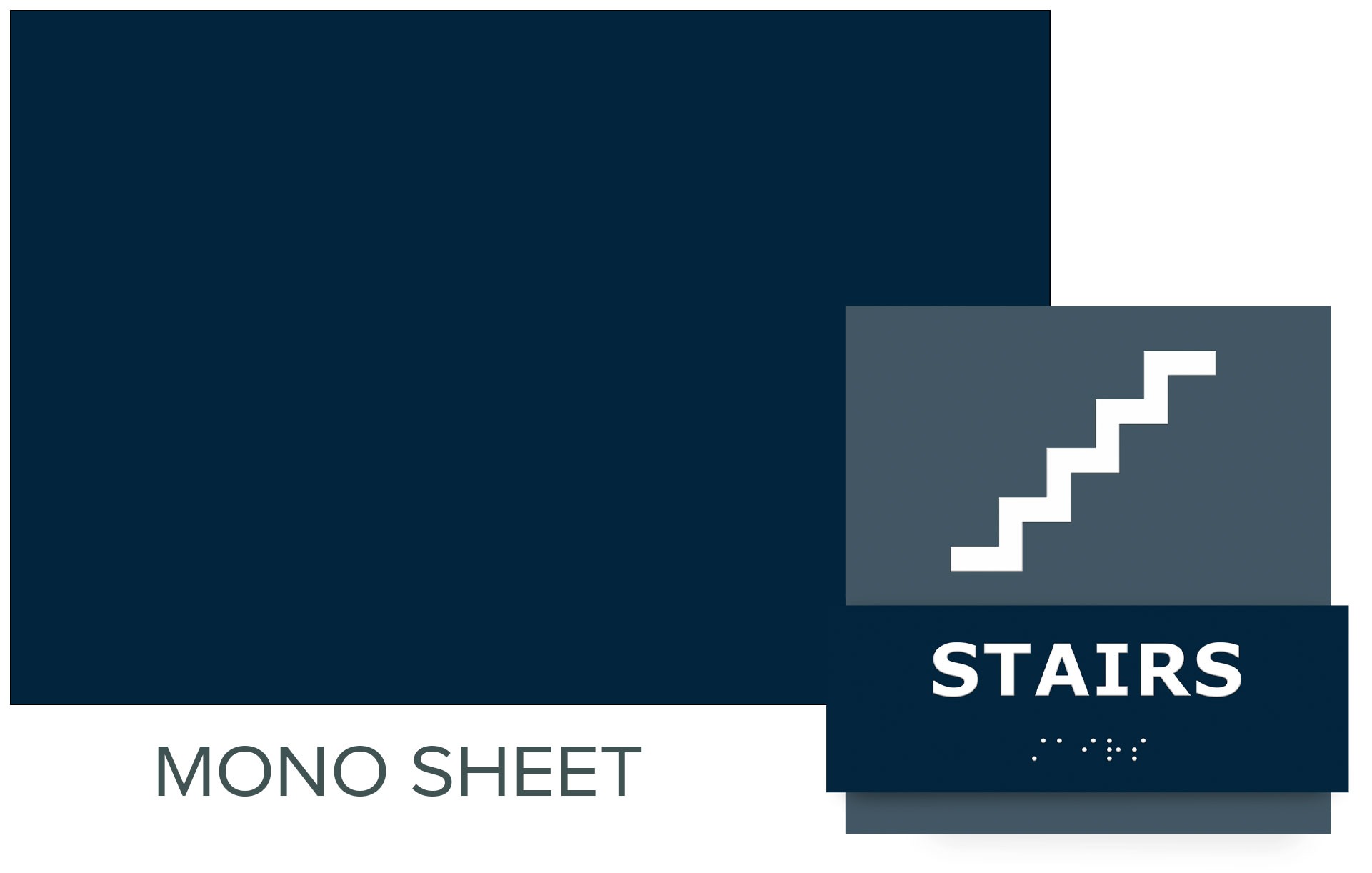
In part three, we’ll take a deeper dive into some specialty engraving materials such as glow-in-the-dark, reflective, heavy duty, fire retardant, and more.