Save Money...Minimize Sheet Warp
If you’ve spent time fabricating any sort of flat plastic sheet material, you’re probably familiar with warp. Depending on the size of the sheet and the fabrication method, warp can leave you with a useless piece of material. Here are some of the factors that can cause warp and some steps you can take to minimize warp before and during fabrication to protect your sheet material investments.
WHAT CAUSES SHEET WARP?
Storing material improperly is the number one cause of sheet warp. Plastic sheet will "cold form" to shapes when stored on edge or across uneven surfaces. The longer a sheet material remains in those positions, the harder it will be to recover the sheet and return it to a flat state.
Most of the raw material used to manufacture plastic sheet for the signage industry are hygroscopic (water absorbing) and will warp to some degree if exposed to moisture for extended periods of time. These issues will be common among many materials and from all manufacturers. The material is not defective, as many fabricators have claimed, and is the inherent nature of the resin used to create the sheet.
According to Lucite, an acrylic monomer supplier, acrylic sheet will warp if exposed to variable temperatures. They further state that changing humidity levels cause the greatest variation. Hence, both variability and moisture are contributors to warp.
Protective removable masking of plastic sheet or the application of adhesives can be another source of warp. Tension of the mask or adhesive when applied to the sheet can induce additional stresses on the corners of the sheet and these stresses are often relieved in the form of curling.
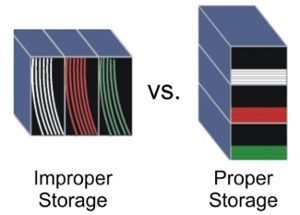
Improper vs. proper sheet storage to minimize warp
PROTECT YOUR INVESTMENT
- Always store sheets lying flat at all times. The number one cause of warp is storing sheets vertically or “on edge.” This causes the sheets to “set” into a curved position. If you have a sheet that has started to curve due to storing vertically, there’s still a chance to save it. Lay the sheet on a flat surface and give it some time. This can help the sheet return to its natural, flat state.
- Avoid storing sheets in extreme temperatures or where there are wide fluctuations in temperature. It’s always best to store sheets as close to room temperature as possible.
- If you’ve got a sheet that is warped, removing the protective masking can reduce tension across the sheet and allow the sheet to relax. Placing an even weight across the sheet (such as additional sheets of plastic) can help speed the process of reducing warp.
- Wait until you’re ready to fabricate to apply adhesive tapes. Sheets stored for prolonged periods of time with adhesives applied can warp as the adhesive material dries out. If you’ve got a sheet that’s warped due to adhesive, removing the adhesive carrier and lying the sheet flat can help reduce the warp.
- Using a mechanical hold-down device can help you save a warped sheet during the engraving process. Clamps can help hold a slightly warped sheet flat during fabrication, but they’ll only help to a point. Since they’re holding the material at the corners, a badly warped sheet may still “wave” even with clamps. Double-faced tape or “tacky mat” surfaces work well. They won’t remove the warp, but they may buy you enough time and hold the sheet down to complete the engraving process.
- When you’re laser engraving, limit the power (watts) or reduce the dpi of raster images. Heat warps plastic, so using a higher power setting than recommended can cause warping during the lasering process. If possible, laser engrave text and graphics before cutting the sheets into smaller plates. Holding down smaller pieces can be tricky, and warp can be greater on smaller sheets.
WASTE NOT, WANT NOT
No one wants to waste valuable product, particularly when you’ve got an anxious customer waiting for you to finish a project. Taking a few precautions before you fabricate and using a few tips and tricks when you fabricate can help you make sure you’re getting the most out of your sheet material.
DON'T FORGET TO SUBSCRIBE TO OUR BLOG!
You can subscribe to the left of this post...right there in the grey box. You'll get a weekly notice of new blog posts so you can stay on top of the latest helpful tips and information.
Have you seen the latest engravable sheet product from Rowmark? ColorShop Woods are here! Take a look at this exciting new product at www.jpplus.com/colorshopwoods